Your cart is currently empty!
Differences Between Carbide & HSS
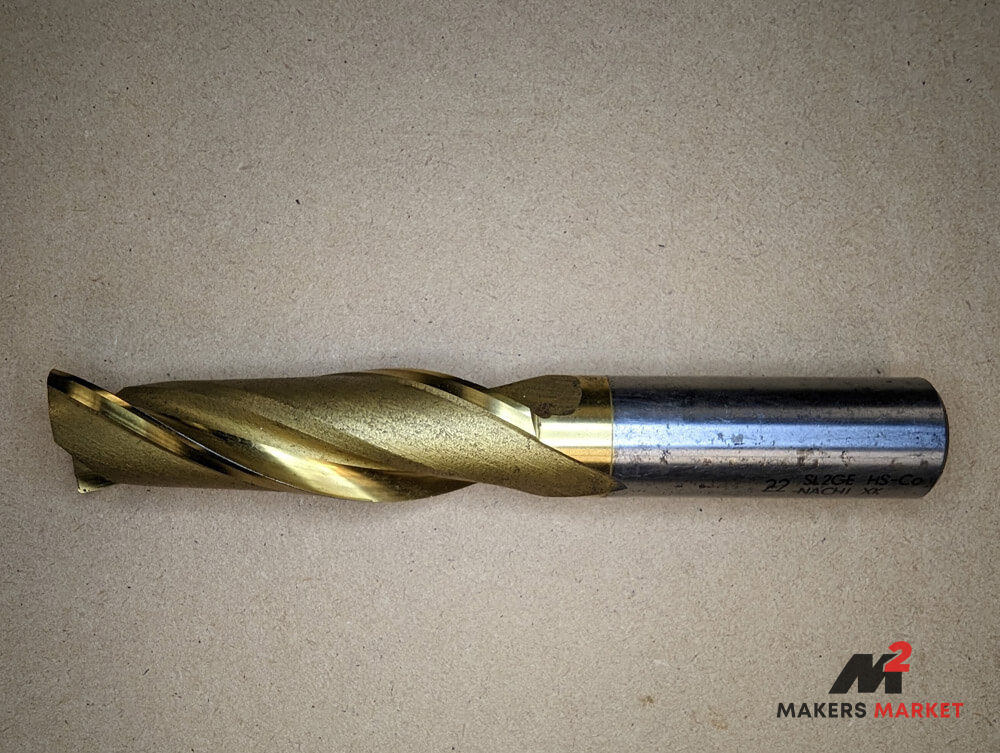
Cutting tools are an essential component in machine shops, as they are responsible for cutting and shaping various materials. Two of the most commonly used cutting tools in the industry are carbide and high-speed steel (HSS) tools. In this article, we will compare and contrast carbide and HSS cutting tools to help you understand the differences between the two.
Carbide cutting tools are made of tungsten carbide, a hard and dense material that is made by combining tungsten with carbon. On the other hand, HSS cutting tools are made of high-speed steel, which is a type of steel that is specifically designed to resist heat and abrasion.
Due to their high-speed steel composition, HSS cutting tools are more resistant to heat than carbide cutting tools. This makes them a good choice for cutting operations that generate a lot of heat, such as drilling and tapping. Carbide cutting tools, on the other hand, are more susceptible to heat damage, which can lead to their degradation over time.
Carbide cutting tools are typically more expensive than HSS cutting tools. This is due to the higher cost of the tungsten carbide material and the complex manufacturing process required to make carbide cutting tools. HSS cutting tools are less expensive and can be a good choice for machine shops that are working on a tight budget.
Carbide cutting tools are more durable than HSS cutting tools and can last longer, especially when cutting tough and abrasive materials. HSS cutting tools, on the other hand, are more prone to wear and tear and may need to be replaced more frequently.
In conclusion, the choice between carbide and HSS cutting tools depends on the specific requirements of the cutting operation. Carbide cutting tools are best suited for cutting tough and abrasive materials, while HSS cutting tools are better for cutting softer materials and operations that generate a lot of heat. The cost of the cutting tool and its durability should also be considered when making a decision.